Meet the Welder - Dave Flew
In the middle of the countryside in the South-West of England there is a garage, Where we meet the welder, Dave Flew. We popped over to meet Dave in his garage but we were not going to talk about cars. Dave has a passion for art and creates sculptures in his spare time.
R-Tech: How did you get into welding?
Dave: When I was at school I was told that I wouldn’t amount to anything. They actually said in my careers meeting that I would be suited to being an undertaker!
I left school in 1995 and went to college in Soundwell in Bristol to study panel crash repair. I was taught to gas weld, MIG weld and how to do lead loading.
I had a flash of inspiration whilst I was at the college that if I was going to have my own garage one day it would probably help if I knew mechanics as well! I could see that there was a cross-over between both disciplines. So a couple of years after that I enrolled at Brunel College and studied Mechanical Engineering.
At school they told me that I had to train in one specific task to do a job, but I didn’t want to do that, I didn’t want to do just one thing, I wanted to do everything! So I went and trained as a mechanic as well.
When I first started in the trade I was doing heavy body accident repair work at a garage in Worle. I worked through a number of garages and learnt many different things along the way. I worked in a classic restoration garage for a couple of years and an engine and gearbox centre for three years and picked up different skills from each of them.
I was always good at doing things with my hands. I think looking back on it if they had explained why I needed to know the things that they were teaching then I would have engaged better. For example, if we had a maths lesson teaching trigonometry and they explained that one of the uses of this is to measure the height of a building then I would have been all over it! I learn by necessity. I had to go back to college to learn how to survey and had to relearn coordinate geometry and trigonometry, which I hated, but it was so much easier because there was a purpose behind it.
R-Tech: When did you learn to TIG weld?
Dave: I am always trying to learn new things. I actually taught myself to TIG weld via YouTube about 6 years ago. I went through about 9 hours of different videos to get an idea of the process and get a handle on it and soaked up a huge amount of knowledge from text books and then I picked up the torch and got started. I have been enjoying it ever since! I don’t even really think about it now, I just turn it on, tweak a few settings and get stuck in. I love to see all the colours that you can get from TIG welding. It was born out of trying to improve my skill sets and get better and with the R-Tech equipment it has been pretty dammed easy. I have used you guys for about 6 years now, can’t fault the service, you are lovely people, the equipment is great and I can’t fault it. The price point of the TIG is fantastic for the amount of machine that it is and what I can do with it is superb.
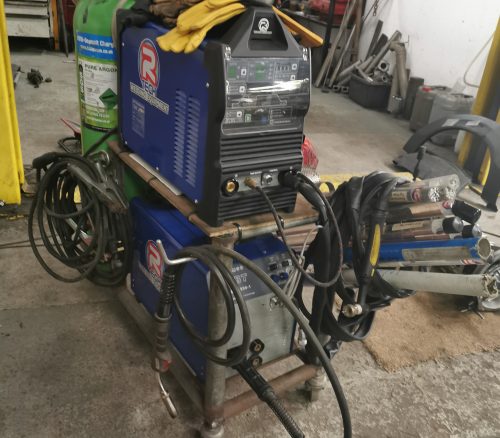
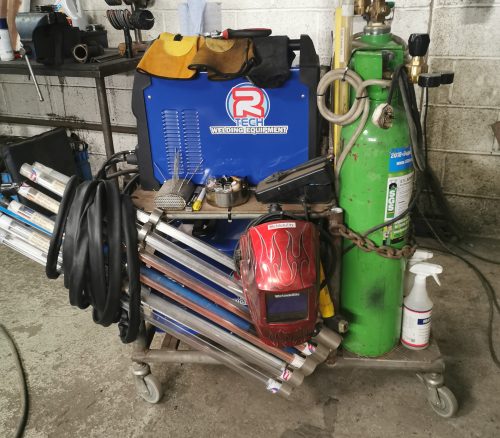
R-Tech: Obviously you run this garage on a day to day basis, but how did the artwork begin?
Dave: Essentially I got bored of welding sheet metal together. I need to learn on the job, different angles, materials etc. So I basically started to weld bits of rubbish together. I went to America in 2016 and this is where my creative epiphany happened! I meet some wonderful people over there that encouraged me when they saw my breadth of skills. The first thing that I made was a twin candelabra made out of a Mini gearbox main shaft and a twin headed stainless steel blow lamp which I found on the pipeline that I was working on about 10 years prior to that! I just liked the look of these two rolled end metal cups; it was scrap so I just picked it up. I made the candelabra for a friend in New York and things have just snowballed from there really.
R-Tech: Where do you get your inspiration from?
Dave: Well there are two sides to that really. Sometimes things are born out of necessity and other things are just kind of ideas. When I am working I am thinking constantly and drawing inspiration from lots of different things. There is never any planning or drawing or sketches of anything that I make before I make it, I picture it in my head, which I have been told is a bit of an odd way of doing things. It is all tucked up in my head and I will develop several different projects all at the same time. I will work out all the pros and cons and things that I may run up against during the build that is going to occur and then embark on it.
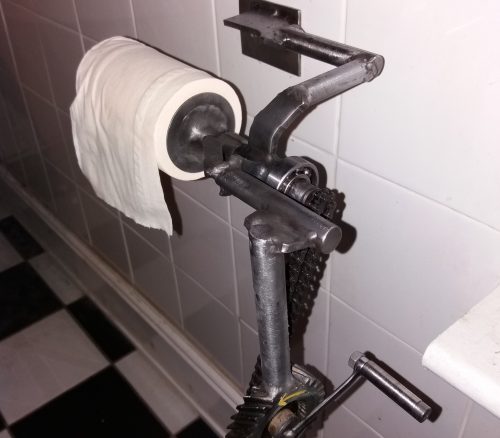
Some of the more mechanical things that I have made were things that I thought it would be nice to show people the inside of a motorcycle engine or a gearbox which I am very familiar at seeing. I thought it would be good to open it up to people who have never seen them. I like the detail and the accuracy of engines and the precision of getting everything right. I have a burning desire for accumulating knowledge and if something takes my interest then I follow that path and see where it leads me.
I made a Union Jack flag and an American flag out of scrap corrugated iron that a local farmer had put by his gate. I drove past it and saw one corner of it was ruined and the first thing that I thought was it looks like an old flag. I asked the farmer if I could have it and he said I could have all of it! So i piled as much of the old rotted metal into the back of my car and got it back to the workshop. I had to make the Union Jack there and then! This is sometimes the way with things, I become almost obsessed with it; I can’t stop until it is done. As I am watching it grow in front of me I don’t want to stop! I get tunnel vision and I really enjoy that part of it, it is my artist mode.
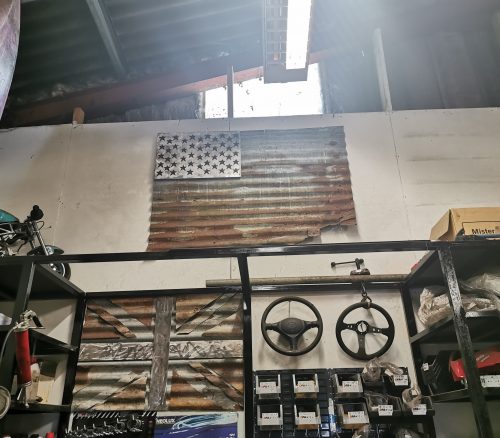
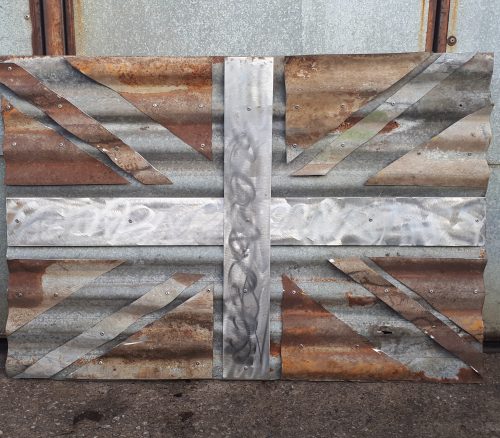
One of the proudest things I came up with recently was how to tightly wrap aluminium TIG rods together to make a metal rope to then make jewellery out of it. I pondered over this for about a week and I was determined not to look up how it was done, I had to work it out for myself! Then I had an epiphany, it was nothing more than placing three ends of the rods in a vice and the other ends in a cordless drill and pulling the trigger and off it went! I then stood there for an hour making these ropes out of twisted aluminium!
I would never claim to be the first to do certain things but it is the satisfaction of working it out for myself. I try not to be influenced by what I see elsewhere, I want what I do to have some kind of authenticity and legitimacy to it.
I don’t want to be categorised as being one thing, I can do anything that people ask for, and I don’t limit myself.
R-Tech: Which pieces have you found the most challenging?
Dave: The Indian Dancer; I had never made a human form before and I only had a 2D picture as a reference so I ended up trying to stand on one leg to try and get an idea of the feel of the pose! It is made out of small pieces of stainless rod and bar which I welded together and then ground into shape. The abrasives salesman came in to the garage whilst I was working on it and said that I was doing it all wrong! I said what do you mean? I have created this, how can it be wrong! Maybe I have created artistic grinding!
When I had finished it, the core of her body was slightly too long, so I had to cut a section out of her about 6-8mm and re-welded her. I think you shouldn't be afraid to go back and cut it up and re-work it if it is not right.
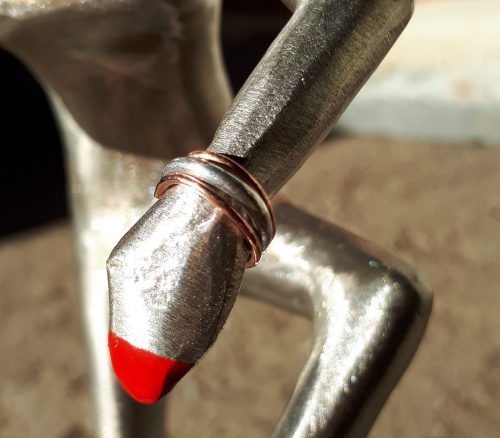
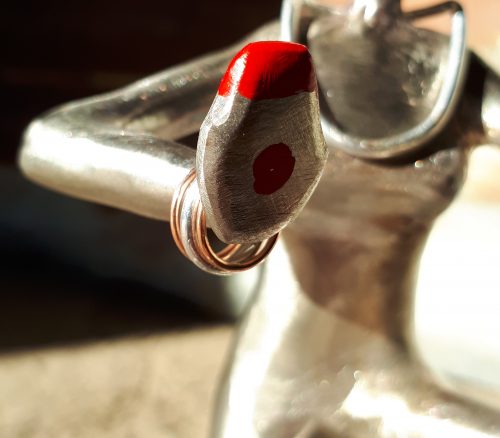
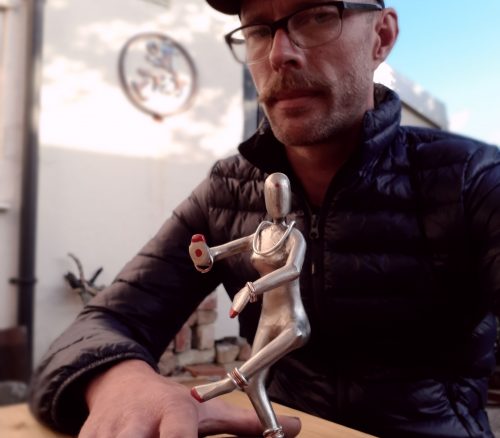
I also made a giraffe with the same process.
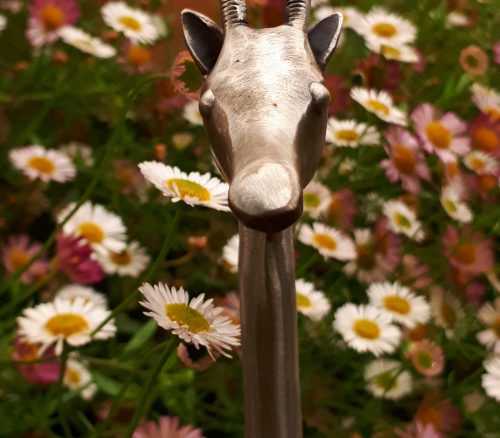
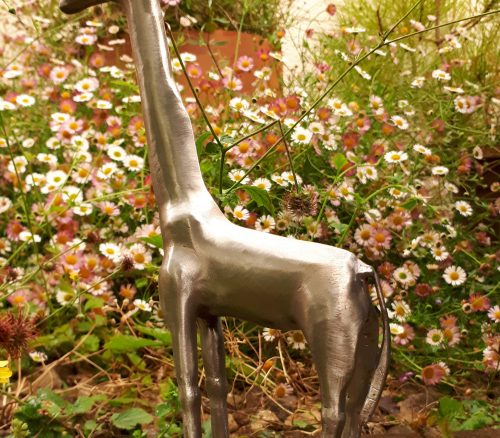
I made a gate for our front garden made from stainless steel so that it will last and have incorporated some of the roses that I have made. The roses take about an hour each to make. I have made the roses out of different metals, there is one copper one and then half of them are stainless and half of them are mild steel so they will age differently. In my body repair work I am constantly fighting against corrosion but now being able to embrace it and work with it is nice, I like the textures of rust and the way that things age.
R-Tech: Tell me about some of your other sculptures.
Dave: This piece was born from the rock itself; I found it on Bude beach. I was on holiday with my wife and I saw this piece of sparkly white granite and I thought to myself that doesn’t belong here, there is no granite along this part of the coast. I turned it over and saw that it had 4 cut marks in it, it had obviously been drilled and prised off a face somewhere, and as it was so smooth it had obviously been in the sea for a long time. When I saw it I couldn’t leave it there, I took it home and put it in the garden where it lived for about 10 years.
I then obtained a bunch of truck ring gears and had some stainless rods. I wanted to make something with it and use the features of the rock. At the time I was fascinated with crop circles, having set out land surveying I am well aware of the difficulty in accurately laying things out, even if you are using 3D GPS, it is very specialised work and even harder to create at night. It is the geometric design that I love and that they conform to the ‘golden rule’ which is a mathematical formula for creating shells and circles etc. That geometric side of it, the lines and the bisecting angles stuck in my mind and in my head I started creating overlapping circles and lines designs and then made this piece.

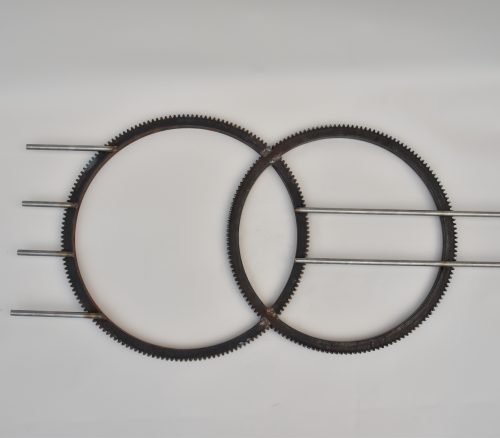
The cow skull is made from a pair of con rods from a truck, a forklift chain and automatic gearbox parts from an Audi.
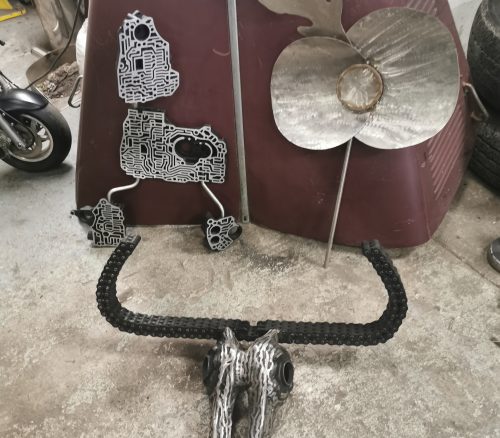
This sculpture is made from Honda gearbox. It displays the fluid path ways in the box. I decided to highlight these by painting it black and sanding the front faces. I have called it untitled because I don’t even know what it is! I just wanted to use the parts and display them because I was fascinated with the inner workings of it.
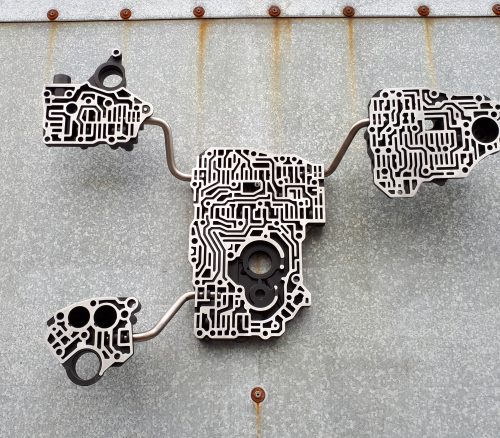
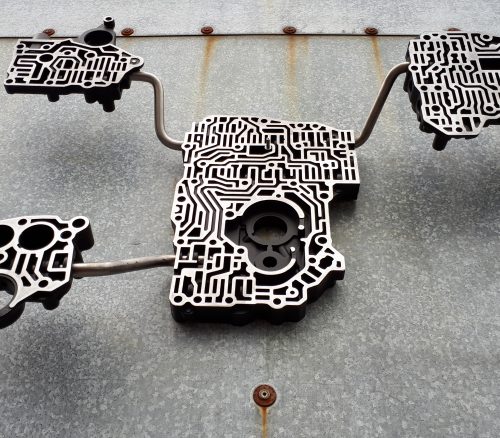
I like to show the inner workings of things to people that would never have seen them, like the motorcycle engine, it came in as a non-runner and was really chuffed when I saw that it had a steel timing chain, so I welded all the links together with my TIG and welded the valves to the followers in the cam shafts so it was suspended above it. This is how it would look on the bike but it is hidden by the faring.
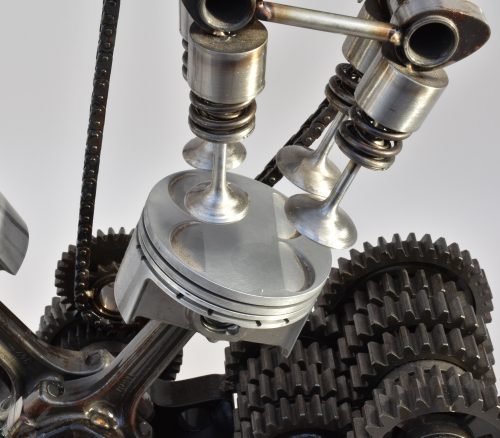
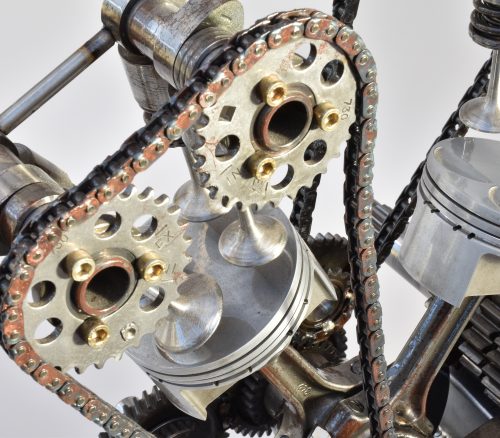
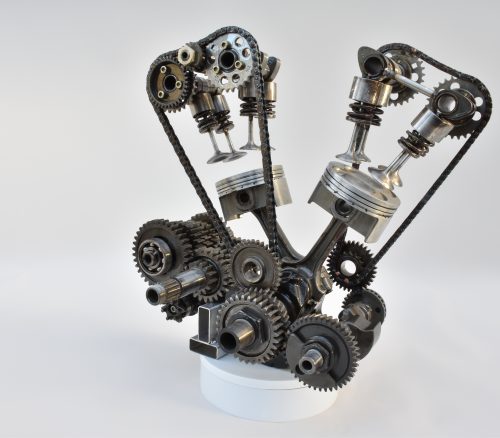
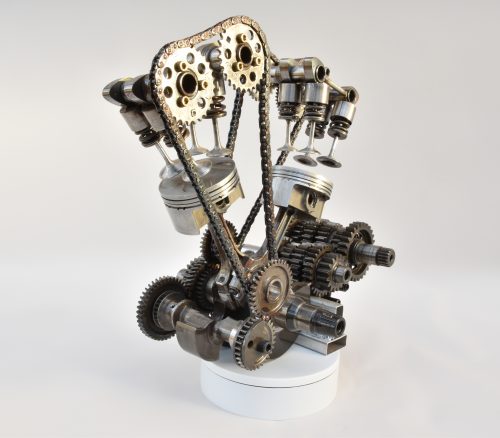
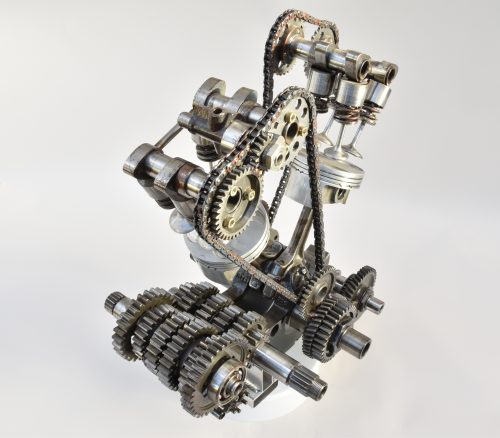
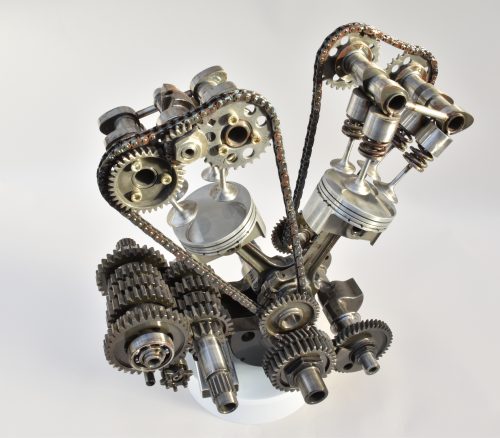
R-Tech: So what is the next project going to be?
Dave: The next piece that I have going round my head, and I am itching to get started on it but I know it is going to take a lot of time and effort to do it, is an Indian twin hand pose called the ‘Avahittha’. I am going to create just the hands and forearms and they will be life size. I am going to have a friend come and model for me so I can try to make them look as close to real hands as I can.
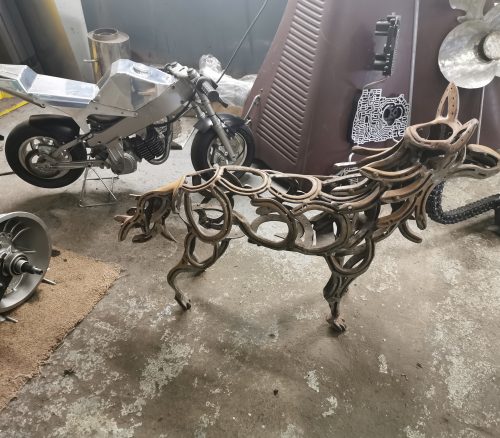
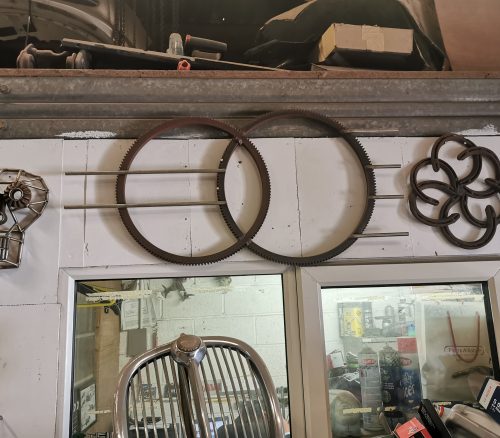
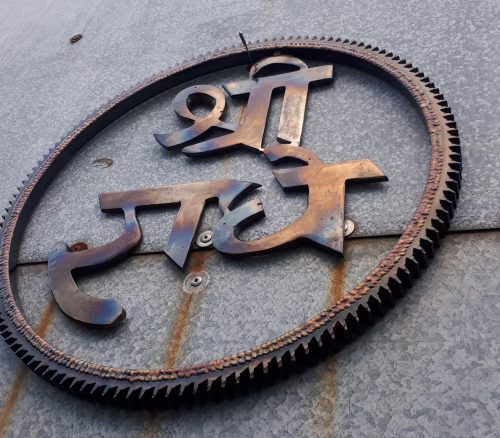

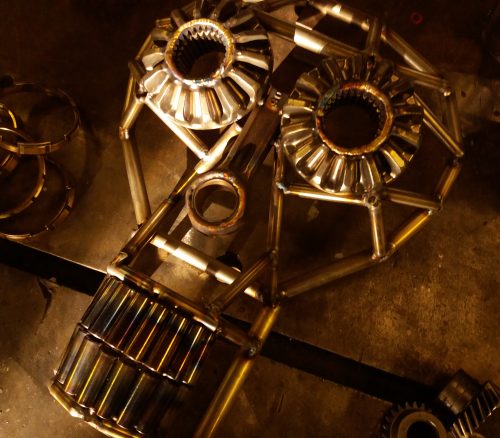
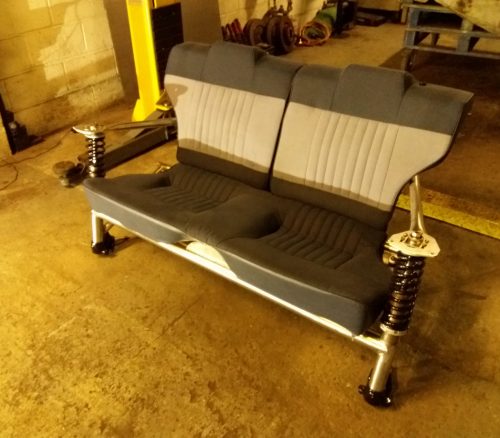
You can see more of Dave's work on his Instagram page @deaf_metal
Do you fancy giving some sculpture work a go? Check out our range of machines to help you get started.