MIG vs TIG Welding
But which one should you choose?
You're after a new welding machine for the list of projects and ideas you have stacking up in your head however, when visiting the website you find yourself jumping from MIG welder to TIG welder and then MIG vs TIG Welding showdown begins.
There are both positives and negatives to both types of machines, they will both stick two pieces of metal together and that's the main thing. We will completely disregard amperage output amperages in this post and mainly focus on the characteristics of both processes. As mentioned before, there are positives and negatives to both processes and at its core can be of the opinion rather than the fact that TIG welding is better than MIG welding for a particular job, and vice-versa.
Below, we will go through the strengths of a TIG Welder and a MIG Welder, along with some points that make that process less ideal for certain applications.
TIG Welding
TIG Welders come in many different configurations, if you take a look at the TIG Welders we have on our website, you will see they come in digital, analogue, DC only and AC/DC models. As previously mentioned we wont be going into to much details about the benefits of having a digital over an analogue or tips and tricks on how to lay down perfect TIG welds, that information can be in our TIG Welding guide if you were interested in that kind of thing.
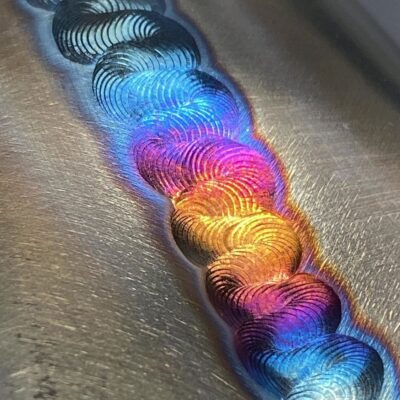
What Are the Benefits of TIG Welding
Welding Aluminum - When welding aluminum, you tend to find this process a lot easier when using an AC/DC Tig welder. You will have much more control over the welding arc which will significantly reduce the risk of burning holes through the work piece. We suggest using a foot pedal when TIG welding aluminum as it greatly increases your control over the arc.
ARC Control - We briefly touched on this above, when using a foot pedal, you have complete control over the power output of the machine. This can be done via the torch switch also, it may not be the same control you would achieve with a foot pedal however it is more than you would have over a MIG welder. By setting the base amps, your maximum amperage and the time it takes for your machine to slope upwards toward that maximum amperage, you can ensure that you are gently applying heat to the work piece. It gets a little confusing but we cover it in more detail here - TIG Welding Guide.
A Great All-Rounder - As you only use pure argon gas for TIG welding, paired with a lanthanated tungsten, you should find it very straight forward to go from welding mild to stainless steel and then over to aluminum without changing a single consumable. Not only is a TIG welder versatile in the material it can weld, it is extremely versatile in the positions you are able to weld in, be this flat on a bench, vertically and horizontally.
Cleanliness - Welds produced by a TIG welder are extremely clean and should require no cleaning, this makes whatever it is your are working on, ready to go as soon as the weld is completed. As TIG welding produces little to no sparks, spatter is significantly reduced. Most machines come with a cleaning function, this is where the arc does a lot of the cleaning without you even noticing. This certainly saves you a lot of time!.
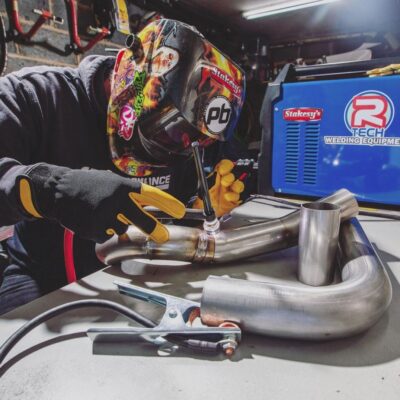
Disadvantages of TIG Welding
It can be slow! - TIG Welding takes time however the time and patience does pay off when you see the results that are achieved. If you are looking for a quick fix however, this is where a MIG welder may be the better option.
It's a steep learning curve - There is a lot of learning involved when it comes to TIG Welding. If you have ever gas welded in the past, you have a head start due to the process being very similar. Once you grasp a TIG machine however, the rewards for your efforts are more than worth it!.
Gasless isn't an option - Gas is required for all types of TIG welding and therefore makes welding outside with the machine a little more difficult if there is nothing to protect you from the wind.
MIG Welding
MIG welding is arguably the easiest of the arc welding processes for a novice welder – and one of the most versatile for a skilled professional, whether you're working in automotive chassis construction or container fabrication. But what are the headline advantages and disadvantages of MIG welding.
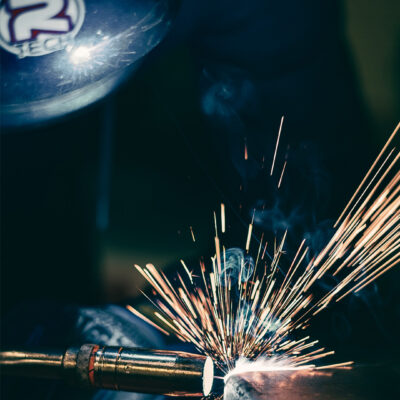
The Advantages Of MIG Welding
MIG Welding Is Fast - With any welding, the time taken has to reflect the difficulty of the join and the quality desired from the finished weld. But, all things being equal, if you put MIG welding up against the other popular forms of welding, MIG is going to win most if the time – whether in the hands of a welding novice or a seasoned fabrication specialist. Why? The answer lies primarily in the continuously-fed electrode, which may be fed from the welding machine, from a spool-gun MIG torch, or in sophisticated industrial applications, through a combination of push and pull feed technology.
Ease Of Use - One day, we’ll find out just how easy MIG welding is for a complete novice when we set our copywriter loose on some gash plate with one of our machines. He had a go at oxyfuel welding about 40 years ago, so if anyone counts as a novice, it’s probably Al. Watch out for the video and blog post in future… But seriously, the one-handed operation of the MIG torch and the automation of several other aspects, make MIG welding easier to learn and gain proficiency with than, say, TIG welding or stick welding.
Fewer Stops And Starts - That continuously-fed MIG electrode scores again when it comes to cutting down the number of times you have to stop and start welding during a job. With stick welding, or even TIG, you’ll be stopping and starting as if you are in rush-hour traffic. What’s more, there will inevitably be adjustments to make and new electrodes to fit before you can re-start that weld. Just like the difference between trying to get to a job at peak time and making the same journey early in the morning, it all adds up. Try it and you’ll see what we mean.
You Don't Need Gas - That's right, you can MIG weld using gasless wire. Admittedly it isn't as clean as welding with gas but it does a good job of it!. This makes MIG welding in the agricultural setting much easier and you also save money on monthly rentals of gas bottles!.
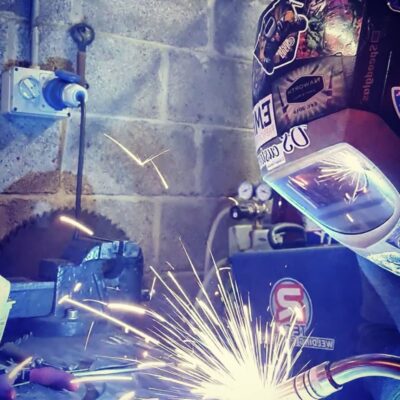
Disadvantages Of MIG Welding
More Maintenance - Okay, a MIG welding machine is more complex than a stick-welding set up and regular maintenance is importance, for safety and quality of welding. But remember again our point about component-level repair and maintenance. Not all machines allow this (R-Tech MIG welders do), but many do. As well as that, if you choose right, your welding machine supplier will lend you a MIG welder while yours is in for a service. We do! Why wouldn’t you?
Weird Positions - If that tricky weld happens to include vertical or overhead welding, the high heat input and mobility of the weld puddle may mean that you need to look at another welding technique. But that’s a small price to pay for all the advantages of MIG welding. Besides, if you choose the right machine, you’ll have stick-welding capability anyway. Problem solved!
Burn-Through - With certain materials, not least aluminium, there is a risk of burn-through if your workpiece is less than .5mm. Up to a point, your skill level may help you get around this, but it's generally accepted that MIG isn’t best suited to very thin materials.